
Evergreen Forest Products - Tamarack, Idaho
Project Date: Fall 2009
Details: Yanke Energy designed, fabricated and installed a new steam and condensate line used to provide steam to Tamarack’s new kilns. The steam is supplied by a boiler in the 6 MW co-generation facility located across the highway from the new kilns. Heat from steam condensate is used to remove ice and snow from the concrete slabs which serve as the input and output aprons of the kilns. The kilns run an average of 10,000 #lbs hour. Yanke was responsible for the mechanical and electrical design and installation of steam line, valve control, and slab heating equipment and controls.
Project Highlights
- Installing 1000 ft of 10” steam line installed from boiler building to new kilns. Steam line routing included a 90' bridge to go over a highway.
- New valves valves were installed connecting the kiln steam feeder line to the exisiting main steam line and also to the first turbine extraction. The controls are designed to maximize the steam coming from the turbine extraction and to minimize the use of main steam to the kilns.
- The kiln input/output aprons are kept free of ice and snow due to a radiant loop heater installed in the concrete slabs. Yanke Energy designed and installed the heating and pumping system.
- Fiber optic cable is used to connect the kiln control room to the boiler control room. Operators use two networked Allen Bradley touch screens to monitor the system. The touch screens allow a convenient coordination between the kiln operator’s steam requirements and the boiler operator’s steam availability.

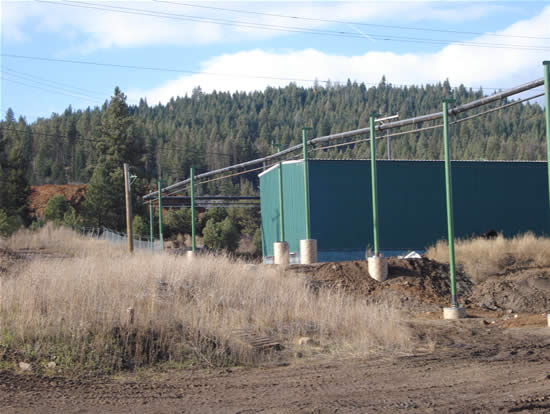
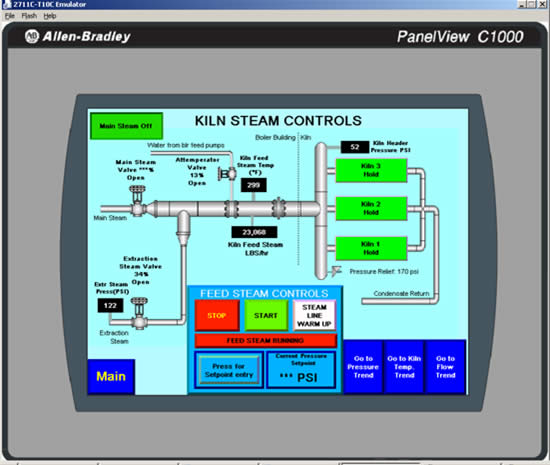